Dome Technology is currently constructing what will be the second-largest clinker storage dome in the world. This dome was designed 220 feet in diameter and 164 feet tall, and perhaps most importantly to the customer, it will contain 190,000 metric tons of clinker.
When complete, it will be second in size only to a Romania clinker dome also built by Dome Technology and will act as an important project in the construction company’s 40-year portfolio.
A project this size doesn’t kick into high gear overnight. Conversations started in 2017, and after pinning down the must haves—maximizing site dimensions, required live reclaim percentage and personnel safety—Dome Technology’s team presented different dome shapes and sizes with innovative solutions to meet customer needs. In the end, the customer chose three on-grade reclaim tunnels to increase the percentage of live reclaim and to accommodate the conveyor layout on the site.
The above-grade tunnels are backfilled with limestone, and the backfill is held below the top of the tunnel hopper so that when the clinker is reclaimed by a wheel loader, the operator can easily reclaim the stored material without accidentally disturbing the tunnel backfill. This “floor” will minimize the likelihood of limestone inadvertently being picked up with clinker product, and it will lower construction costs too, Dome Technology sales manager Lane Roberts said.
When complete, the major benefits of this dome will be seen in construction and maintenance cost savings. Rather than an aluminum or steel dome roof atop a concrete wall, Dome Technology builds a monolithic reinforced-concrete dome without seams, so moisture entrance isn’t an issue because there are not access points. Also, many foundation systems complement concrete domes, which often cuts costs.
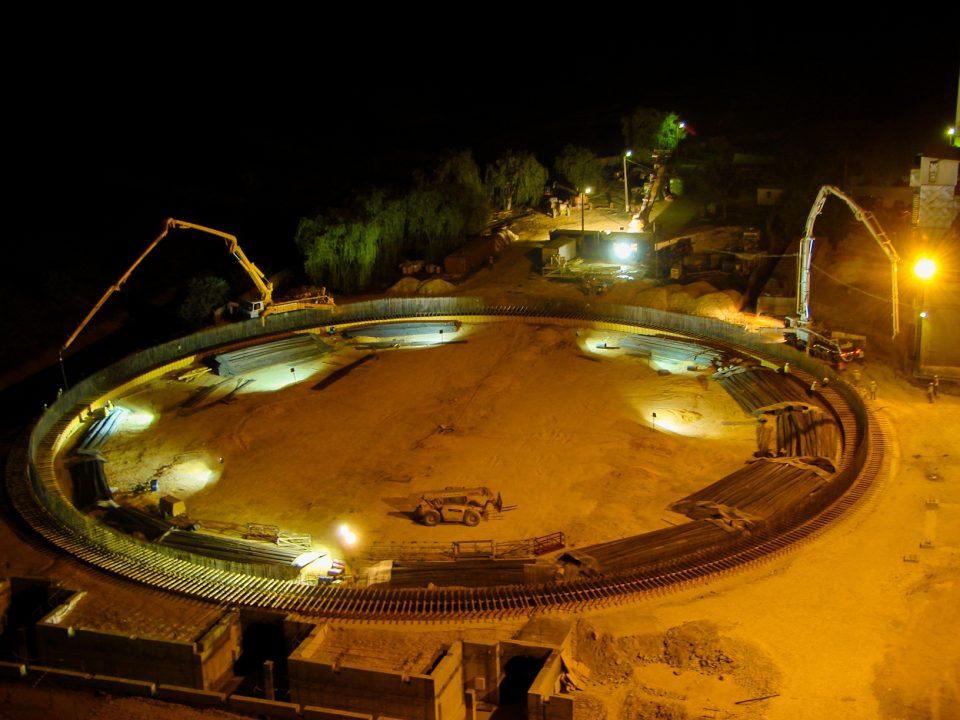
A cement-storage dome’s specifications are limited only by a customer’s imagination. Today’s options include a model with drive-through capability, one for space-restricted sites, and another that maximizes large parcels of land where height restrictions are a concern. But new ideas are encouraged and embraced, and since each dome is custom designed, each has its own look and function. Dome Technology was founded by an inventor, and the pursuit of new ideas is an important company tenet.
“We certainly consider (customer) ideas and look at the merits—we don’t have any issues with someone coming up with a better mousetrap. It’s their project, and we are happy to work with them and advance the technology,” Roberts said. “If it’s a great idea but we can add some extra value to it, we will share that with them. We have a tendency to be really open, to help the customer.”
Better cement storage
Three dome styles are popular with cement companies. The most common is the DomeSilo, a model that’s taller than it is wide and allows companies to stack product deeper on a smaller footprint, requiring less property at the site. The increased capacity is made possible by geometry: The double curvature of a dome lends itself to the ability to build up, rather than out, and the curve provides strength at all points of the structure, even at the apex. The entire interior can be used to contain product.
In recent years Dome Technology introduced a Drive-Through DomeSilo to the marketplace, a model that allows companies to fill truck or rail directly from the storage structure and speed up the process of product reception to delivery. Continental Cement Company was the first to adopt this model, and in 2018 a Drive-Thru was built at a recently acquired Continental Cement site in Memphis, Tennessee, USA. While the existing silo and adjacent scale had not been used for some time, complete upgrades of these assets along with a new dome, barge unloader and dock upgrades have allowed Continental Cement to become the leader in service in the Memphis market.
The company has been pleased with the efficiency of the overall system, said area supervisor Dustin Whited. “We can load trucks at the same time we can replenish our inventory via barge unloading—all of this while being basically dust free, which is important to our customers and to our community,” Whited said.
With dimensions of approximately 100 feet tall and 50 feet in diameter, this Drive-Thru can be supplied by barge from any one of Continental Cement’s plants. The engineering design of the new barge unloader allows discharge into either the Drive-Thru DomeSilo, storing 5,000 tons of cement, or the 3,000-ton traditional silo. New aeration of the existing silo allows for a much-increased truck-loading rate.
The Drive-Thru delivers 100 percent live reclaim from a fully aerated floor. Product flows through a hopper for loading into truck and, potentially in the future, rail. An in-line lump crusher on the loadout stack-up ensures that lumps passed through the receiving system do not make it into trucks. The dome can receive 350 mtph from the barge unloader and load out at 320 mtph. According to Whited, the biggest advantage of this model is the ability to load directly from the floor of the dome.
The third dome model Dome Technology continues to build is the hemispherical dome, particularly at sites with a height restriction. These domes are essentially a sphere sliced in half. These structures are the original dome storage model and are also an economical solution.
Reducing the size and cost of the reclaim system also plays a major part in overall project cost. This often helps determine the most economical dome geometry and efficient storage solution.
Dome storage benefits
Storage is often one of the largest components in any new facility, and a dome is built with an unlimited lifespan—its concrete shell and geometry boast unrivaled strength. Dome construction methods require no interior trusses, so the entire inside volume can be utilized for storage or reclaim systems.
All domes provide ideal conditions for stored materials requiring a controlled environment. Monolithic concrete construction, coupled with a fabric membrane surrounding the entire dome, prevents water and moisture from seeping in. The dome’s insulated nature reduces heating and cooling of the walls and air inside, preventing condensation from forming on the interior. Foam and concrete provide humidity control and moderate externally generated temperature fluctuations.
A dome’s strength and geometry also provide a tolerance for differential settlement. Those qualities combined with geotechnical engineering and site analysis ensure proper foundation selection and performance.
Design build: The key to custom storage and turnkey construction
Based on customer must-haves and a firm budget, Dome Technology can execute an entire project from design to completion. After more than 40 years of experience in bulk construction, the company’s network of bulk-storage vendors and subcontractors is wide and deep, allowing the team to partner with industry leaders.
To start a project, a customer provides a list of required features, objectives and constraints; Dome Technology then provides value-design concepts backed by many years of engineering and construction experience. The customer and Dome Technology work together to optimize the design and project cost to achieve the facility a customer needs within budgetary constraints. These factors guide early conversations:
- Capacity requirements: How much cement needs to be stored and transported annually?
- Geographical and geological position: Define the site requirements and determine the site-specific geotechnical information.
- Expansion: Is this a project extending a facility’s original scope? Is future growth likely?
- Product consideration: A turnkey builder like Dome Technology can provide counsel on designing unique storage for each specific stored product.
- Operations: What are the company’s plans for filling, reclaim, product management and controlling inventories? If these aren’t known or defined, help is available.
Two major advantages with design-build are that change orders are reduced and schedules are usually met because each phase of the project is built into the plan. These often yield cost savings and a smoother construction experience.
Besides costing less to build and operate, domes are also cost efficient. Domes are built with locally available concrete and reinforcing steel, and local crews are often hired for assisting in construction, a benefit for city economies as it provides jobs and pumps money back into the marketplace. Also, a dome’s double curvature requires fewer construction materials with significantly less waste, and a dome can be built quickly; one the outer weatherproof membrane is in place, construction moves inside and continues regardless of the weather.
Construction in the cement industry
If Dome Technology’s current project list is any indication, there’s no slowdown in sight for the cement industry. The company is working on four cement or cement-product projects right now and in conversations for multiple future contracts. With sophistication on the increase, customers can secure the facility they want, and the process is made easier by selecting a construction company that can oversee the project from start to finish.
By Rebecca Long Pyper for Dome Technology
Editor’s note: This article was published in the 2021 BMHR issue of World Cement.