As more coal companies find themselves tasked with covering ground piles, the need for reliable, sealed coal storage is on the increase. Dome Technology’s bulk-storage domes, some of which are DomeSilos™ while others are more hemispherical, provide this kind of security but also are engineered with environmentally friendly features that will satisfy companies and governments for decades to come.
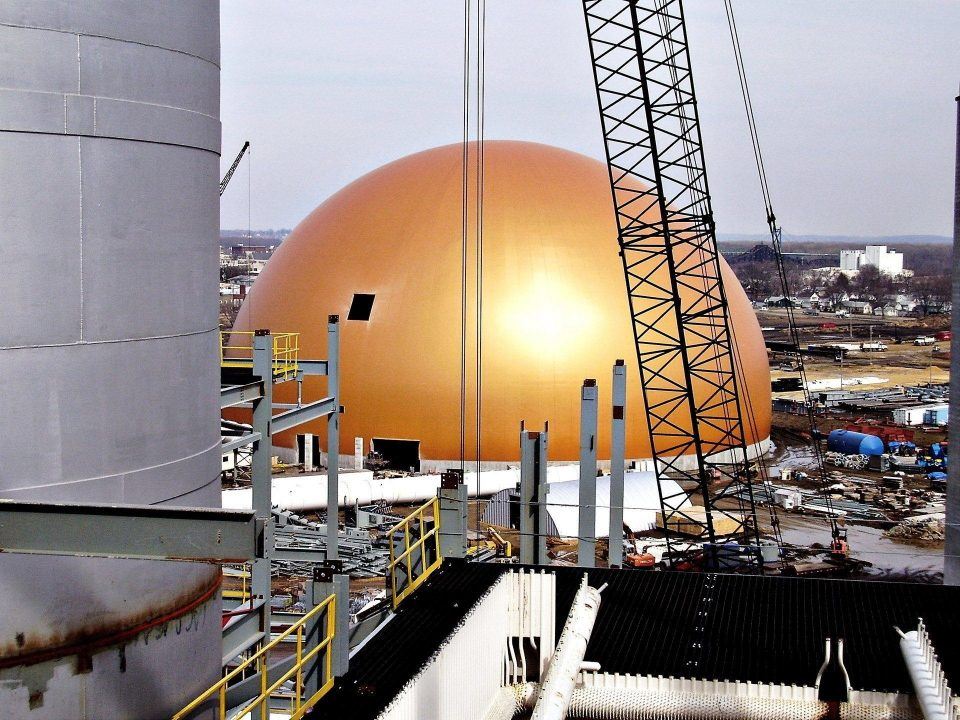
What is a dome?
A dome’s robustness comes from its construction materials. The airform acts as an impermeable membrane to keep moisture at bay. The steel-reinforced concrete shell provides insulation and climate control inside. Combined with steel reinforcement and nature’s perfectly strong shape, domes are well-suited for weathering any storm.
These qualities allow the dome to tolerate frequent loading and unloading. A dome’s tolerance for cyclic loading and unloading is high because of its structural integrity, compared to steel silos built with fasteners or welded seams.
At sites where settlement is a concern, domes can be designed to tolerate some movement; however, there may be other solutions besides deep (and expensive) foundations. Dome Technology helps customers explore options that often reduce costs by selecting an innovative foundation solution that delivers necessary support at the base. That also means less disturbance of the environment.
Due to the inherent strength of the dome and its efficient structural shape, virtually the entire structure can be filled with coal, maximizing storage capacity and minimizing overall project costs compared to other structures.
The benefits of these features are obvious, but what is less clear is how a dome inherently provides environmental protection too. Seamless construction and innovative dust-removal systems keep coal where it needs to be and prevent contamination of the site.
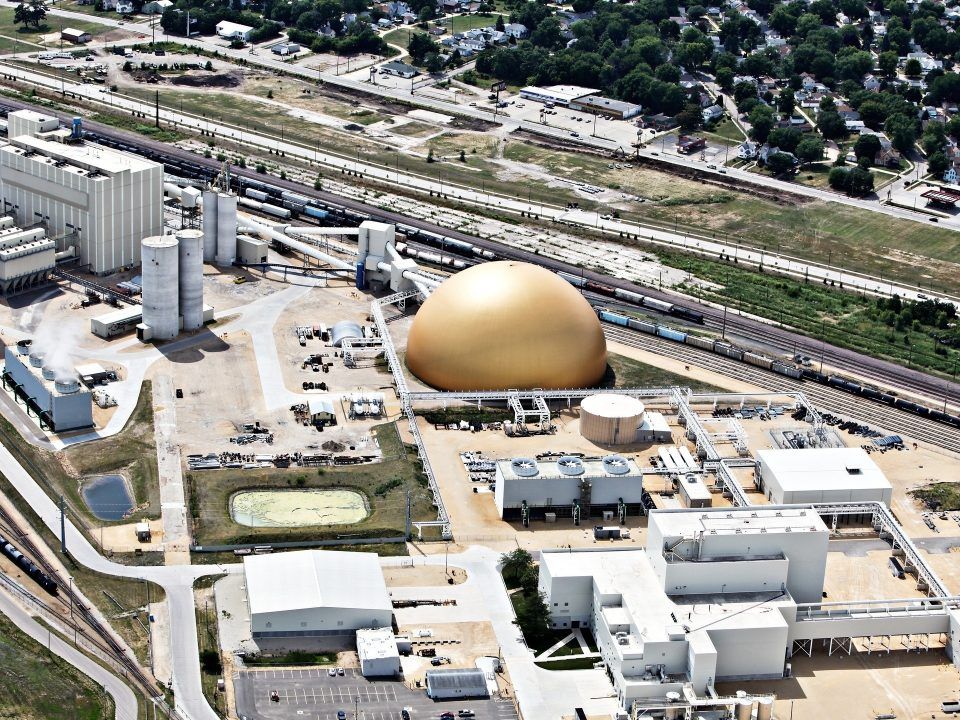
Sealed and secure
The PVC airform covering the entire dome structure provides waterproofing—what’s outside can’t get inside and the opposite is true too. This airform prevents fugitive dust from escaping through joints or seams because there aren’t any in a monolithic dome.
This degree of protection was a main reason ADM chose a dome for its coal cogeneration plant in Clinton, Iowa. According to ADM Clinton Cogeneration plant manager Kevin Duffy, ADM has always stored coal inside some sort of structure to manage dust. But selecting a dome from Dome Technology was an improved means of maintaining coal quality. The dome’s seamless construction protects coal since “you don’t get rain, (and) you don’t pick up the other moisture from weather events,” Duffy said.
The dome is airtight except wherever penetrations are made, aiding in the containment of inert gases pumped inside to minimize available oxygen for fueling fires.
The structure itself can survive a disaster other types of storage might not and will likely reward customers with insurance-premium savings. A dome has inherent strength other bulk-storage structures do not. Should an earthquake, tsunami, or tornado occur, the structure has a better chance of survival than a traditional building, and the product inside will not be introduced into the environment.
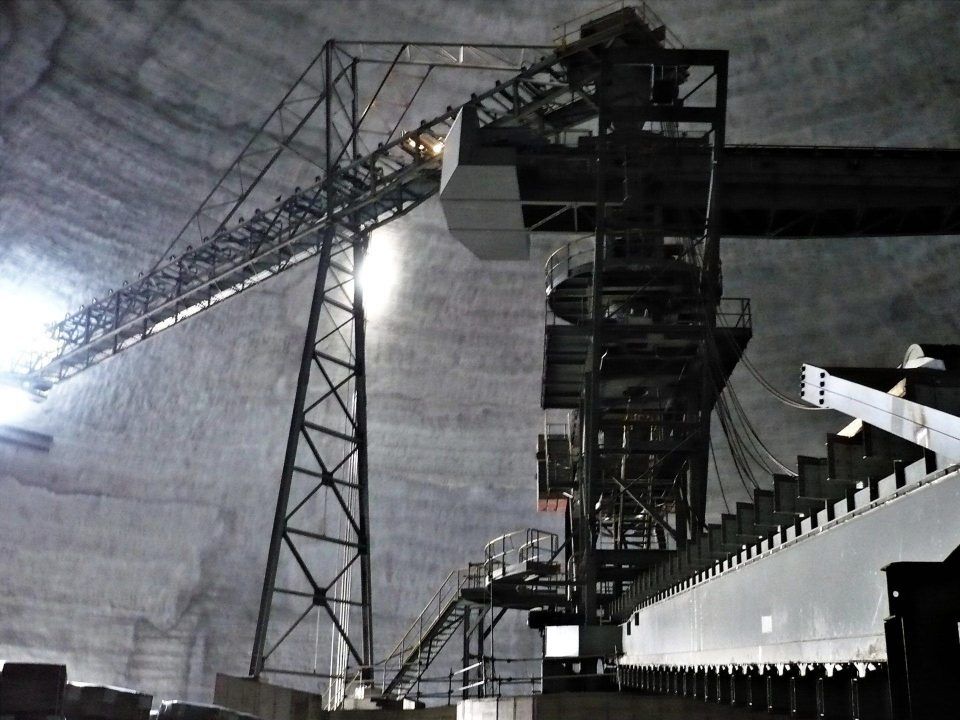
Minimal dust build-up
Since domes are built without the use of interior supports, dust build-up on trusses isn’t a concern. Secondary explosions — the kind caused when initial explosions shake loose accumulated coal dust — are less likely because the support-free domes have no ledges for dust to build up. This advantage alone was one of the most attractive feature for China Coal, who built six domes with Dome Technology. “One of the major dome advantages is to prevent fire because there are no interior shelves to collect dust, and China Coal liked that a lot—for them it was a big deal,” Dome Technology CEO Bradley Bateman said.
How collected dust is dealt with
Managing dust is essential to protecting the environment, and again the dome provides the first line of defense. Sealed and seamless, dust is contained inside and cannot be released into the atmosphere or environment.
Beyond the storage structure, a host of dust-control systems exist in the marketplace. One option is a spray-down system that sprays coal with water to wet the dust, preventing it from becoming airborne. Because water decreases coal’s useful BTU value, this systemis not popular. One variation is to spray oil onto coal instead of water; the dust is still managed, but the useful BTU values are not reduced — though companies must assign a portion of the budget to purchasing oil.
To collect dust within the dome, a wet extraction system is the preferred approach because it “essentially pulls the dust through a water system so it becomes wet, and that’s what pulls out the dust rather than a bag, so now the dust is wet and not nearly as combustible,” engineer for Dome Technology Adam Aagard said. The system pulls the dust through a duct until it can be removed from the facility or destroyed. The scrubber is an attractive alternative to a baghouse system that pulls particulates through a fabric filter, thus collecting dust and storing it in a high concentration where the chance of combustion is still real.
Automatic dust-collection systems can be designed to convey dust away pneumatically via belt to a combuster. Alternately, dust can be collected in a bin or super sack to be hauled away.
Editor’s note: The preceding is an excerpt from a piece published in the Winter 2018 issue of Dry Bulk by Rebecca Long Pyper for Dome Technology